Tracing Risk in Silicon Supply Chains
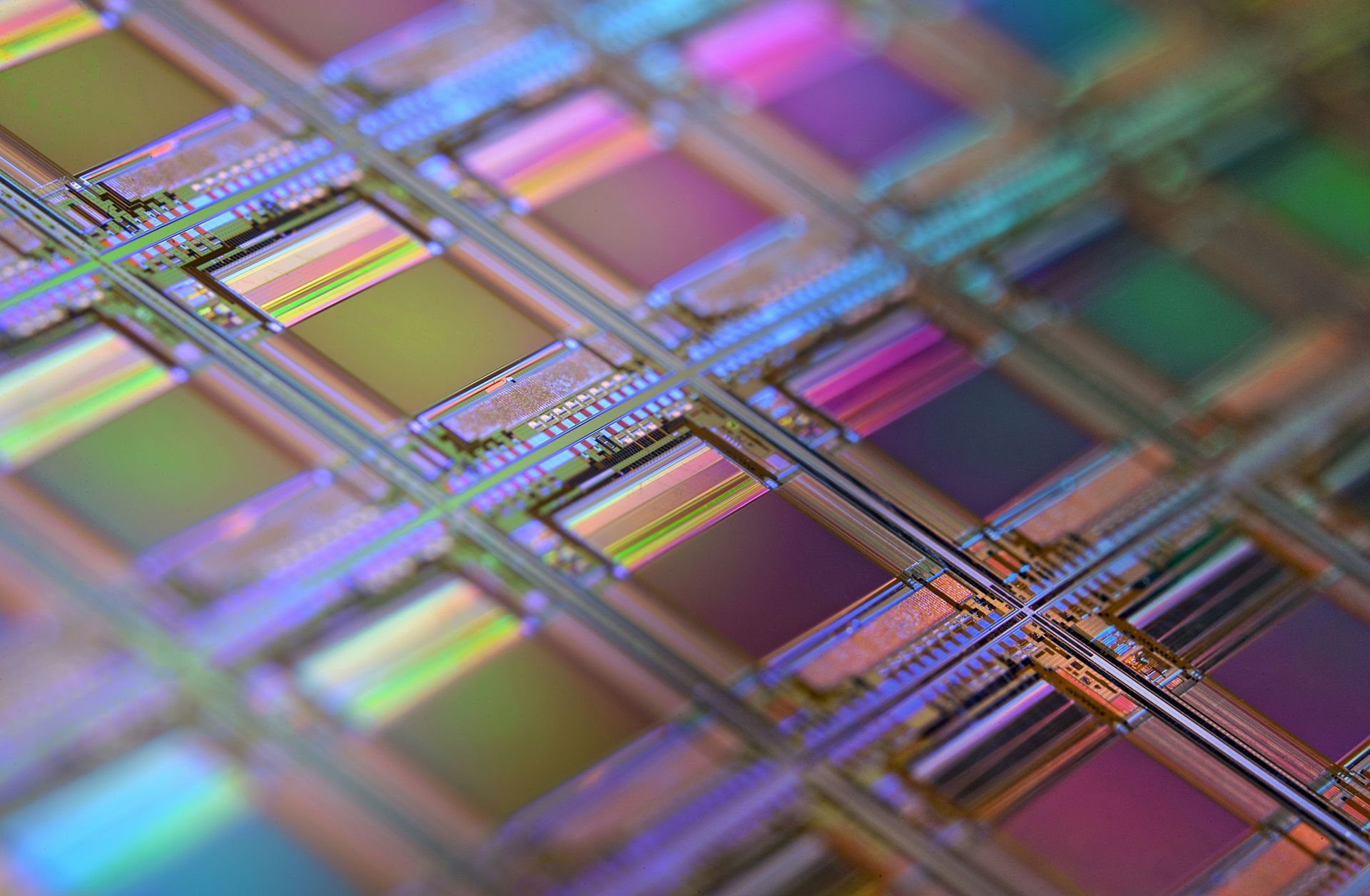
Silicon is used in semiconductors powering electronics and the solar panels driving the energy transition. Extracted from quartz and refined into high-purity forms, silicon is transformed into wafers used in everything from smartphones to solar farms.
But behind its revolutionizing role lies a troubling supply chain increasingly scrutinized for links to forced labor, particularly in China’s Xinjiang region.
From quartz to wafers: A brief look at the supply chain
The silicon supply chain begins with the mining of silica-rich raw materials—primarily quartz or sand—which are refined into metallurgical-grade silicon through high-temperature smelting with carbon.
From there, the silicon is chemically purified into polysilicon, an ultra-high-purity form essential for manufacturing solar cells and semiconductors.
This stage is both energy-intensive and highly centralised: over the past decade, China—particularly the Xinjiang Uyghur Autonomous Region—has become the world’s dominant producer of solar-grade polysilicon, accounting for nearly half of global supply at its peak.
It is here, in the polysilicon production stage, that the clearest forced labor risks arise.
Multiple investigations have documented the use of state-run labour transfer programs that coerce Uyghur and other ethnic minority workers into employment in polysilicon plants under threat of detention.
Companies operating in Xinjiang benefit from low-cost electricity and state subsidies, making the region attractive for industrial-scale production.
Forced labor risks may also appear earlier in the supply chain—such as in quartz mining—particularly in regions with weak labor protections, though evidence there is more fragmented.
Once produced, polysilicon is cast into ingots and sliced into wafers, then integrated into solar modules or semiconductor components.
Because many downstream manufacturers rely on opaque or multi-tiered supplier relationships, forced labor in one upstream node can contaminate entire supply chains, especially when documentation is inconsistent or intentionally vague.
While China dominates the sector, other key producers of silicon and polysilicon include countries such as Germany, the United States, Norway, Malaysia, and South Korea—regions that generally operate under stronger labor and environmental oversight.
Understanding risks associated with silicon
Solar manufacturing remains the focal point of concern. Xinjiang has supplied as much as 45% of the world’s solar-grade polysilicon in recent years. That material is used by dominant module manufacturers whose panels are widely sold in Europe and the Americas. Even when companies operate outside Xinjiang, they may source wafers or silicon metal from suppliers who do not disclose raw material origins.
Semiconductor firms are generally less exposed. The purity requirements for chips mean that most polysilicon is sourced from countries such as Germany, Japan, or the United States. However, indirect risks—particularly in passive electronics or lower-tier suppliers—still exist, especially when component sourcing is opaque.
Automotive companies, including electric vehicle manufacturers, sit somewhere in the middle. They rely heavily on electronics and alloy materials, yet rarely engage directly with raw material producers. This makes traceability more difficult—and due diligence more important.
Sanctioned entities
Public attention has often centered on high-profile solar firms. But upstream, a wider group of Chinese companies—including Daqo New Energy, Xinjiang GCL, East Hope, and Xinte Energy—have been tied to state labor transfers.
Some are under U.S. sanctions. Downstream, their polysilicon feeds into global supply chains via manufacturers like
LONGi, Trina Solar, and JA Solar.
Western firms that source solar modules or electronic components from these companies are now under pressure—not just from the public, but also from regulators—to verify their supply chains.
Traceability or illusion?
To navigate tightening laws—such as the
U.S. Uyghur Forced Labor Prevention Act
— some firms have begun bifurcating their supply chains: using non-Xinjiang material for products destined for Western markets, while continuing business as usual elsewhere.
While this reduces legal exposure, it does little to address the root problem and creates space for bad actors to infiltrate global supply chains undetected.
Supply chain opacity remains a major hurdle. In Xinjiang, third-party audits are impossible due to government interference.
Many suppliers do not clearly disclose the origin of their raw materials or the identity of upstream facilities. Documentation, when available, is often unverifiable.
This structural opacity makes it difficult for even well-intentioned companies to be confident in their sourcing.
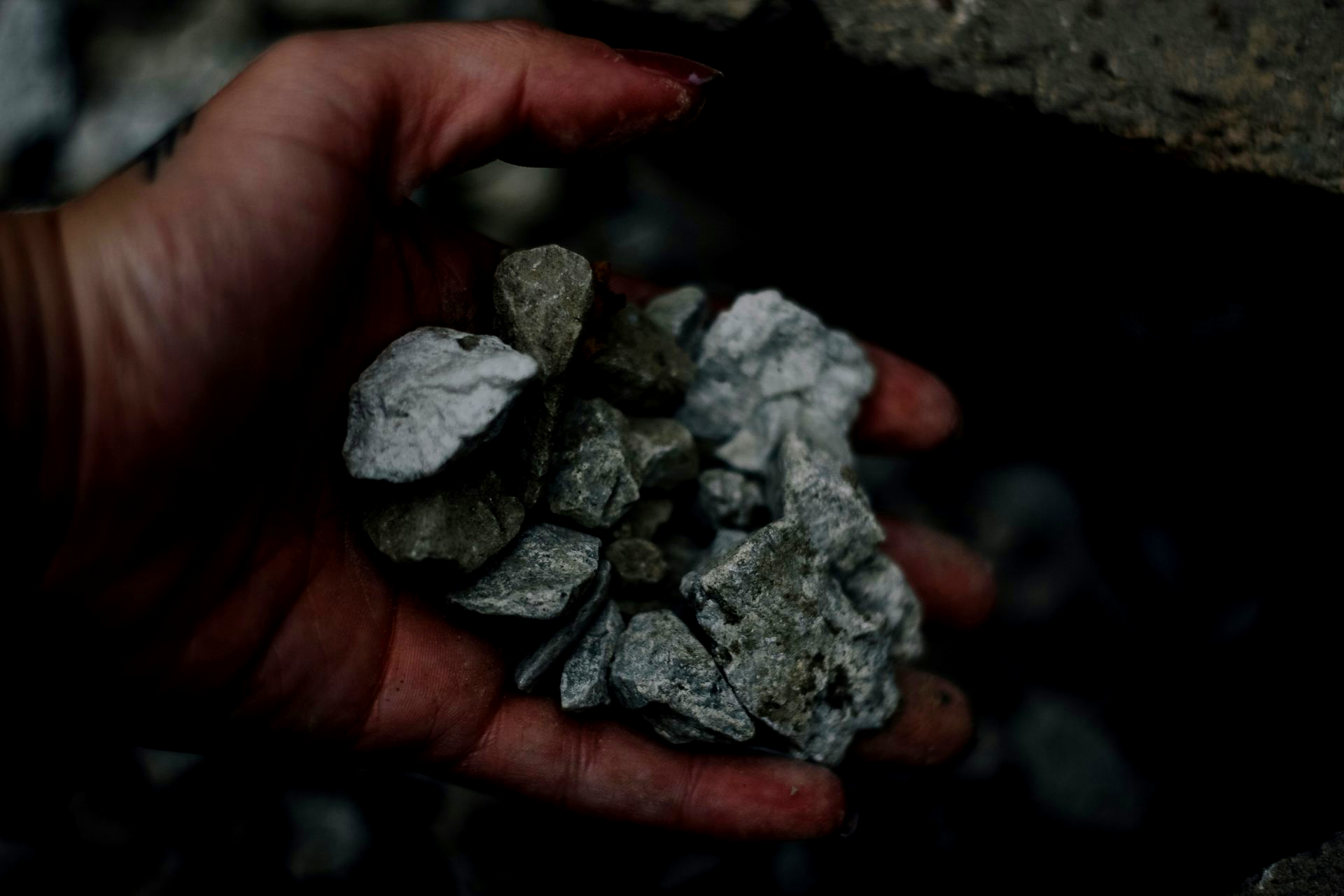